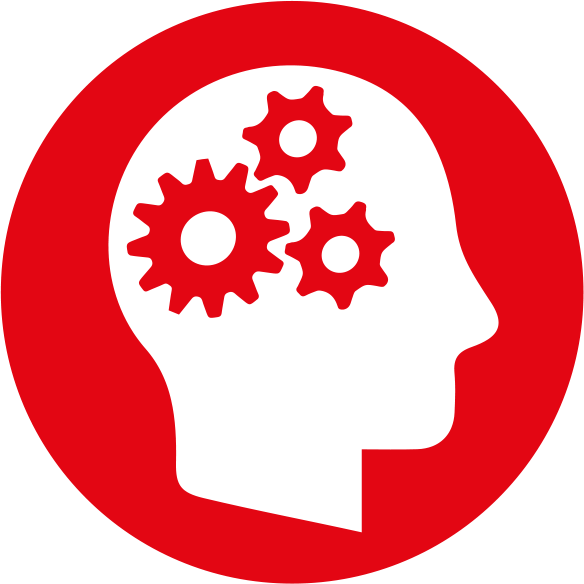
Kalmar Start-Up Services guarantees the right people, resources and processes are in place to support your service and maintenance operations from day one. From large-scale terminal automation to specialist industrial projects, we will work with you to make sure your new operations start-up is a smooth one.
Click on the process chart to see how we can help define your operational processes, service and maintainance needs and resource requirements.
From our experience, the first task is to review your current approach to service and maintenance and compare it to your future requirements.
There are three different approaches to be taken into consideration. These are:
Once the right service and maintenance approach has been identified, a full service and maintenance strategy can be developed for your business.
This is a list of all the tasks that need to be completed to execute the chosen service and maintenance approach. It contains information about the man-hours, skill sets, tools and parts required to complete each task.
Workshop requirements are identified once the maintenance task list is completed. You will be able to see exactly what tools, equipment and parts are needed in the workshop to fulfill the identified maintenance tasks.
This will help to design the layout of the workshop, including washing bays as well as areas for oil separation and the handling of hazardous materials.
Parts inventory requirements are identified once the maintenance task list is completed. You will be able to see which parts are needed to complete each maintenance task, and assess their criticality through a fault tree analysis of equipment. This will help set the precise inventory levels to keep your business running optimally.
As a part of inventory planning you will need to:
The software management plan will make sure your systems are running as expected and include the processes, policies and procedures for updates, testing, emulation, backups and the integration into other systems.
As part of overall software plan, the recovery and continuation processes will be defined to maintain critical operations if an unforeseen system interruption occurs.
It is important to define and document the processes for your chosen level of maintenance before the project becomes operational. In addition, the operational processes for exception handling, KPIs, health, safety and environmental strategies need to be documented.
Once you have agreed your maintenance task list you can define and document the actions that need to be taken for each task. This will make sure that each task is completed efficiently and effectively.
Having a plan in place for handling exceptional situations is essential. The best way to start this process is to map out all the known exceptional scenarios that might occur. Next, develop the plan and processes on how to manage these situations.
To ensure your maintenance team clearly understands the level of service they are expected to provide, a set of key performance indicators (KPIs) needs to be developed.
KPIs will define the criteria the maintenance team will be assessed against, as well as the methodology and tools used to make this assessment. It should also contain the KPI reporting frequency, in addition to evaluation and follow-up processes.
Health and safety strategy will help prevent accidents and injuries. This strategy needs to be developed in line with the health and safety regulations under which your business operates. Once the mandatory permits have been identified, you must ensure compliance with all their requirements.
Operating safely and within local regulations and environmental guidelines is critical when maintaining equipment. Your environmental strategy needs to be documented, covering both risk assessment and the recovery process for any waste or hazardous materials that are handled while maintaining equipment.
Developing a comprehensive resource plan will ensure the right skills and resources are available in the right place for your business to operate effectively.
The resource plan should also identify the training required to build an appropriately skilled team.
The required skills and competencies are defined in the maintenance task list. This includes identifying the right permits, licenses and certifications needed for each individual.
From this information, your personnel’s current skillsets can be compared against those required, and you can identify what additional training and qualifications are needed.
Before recruiting new staff, it is important to identify the skills and competencies that are currently existing in-house. From this, you can perform a gap analysis; the skills you already have versus those that are required. This information will form a critical part of competency and skill mapping analysis.
Before recruiting new staff, it is important to identify the skills and competencies that are currently existing in-house. From this, you can perform a gap analysis; the skills you already have versus those that are required. This information will form a critical part of competency and skill mapping analysis.
From skill mapping analysis and expected staff turnover rates, you can identify the training or retraining your personnel will require. This allows you to develop a full training plan for the future.
Download our white paper “Maintenance of Automated Terminals”, which takes an in-depth look at what needs to be taken into consideration during a greenfield or brownfield project delivery so that your maintenance operations are running optimally from day one.
By accessing the Internet pages of Cargotec Corporation's business area Kalmar (hereinafter referred to as "Kalmar") at www.kalmarglobal.com, or any of its sub-sites (hereinafter referred to as "Site"), you agree to the following terms and conditions. You must not access this Site if you do not agree to all of the following terms and conditions.
Subject to the terms and conditions set forth herein and all applicable local laws and regulations, Kalmar grants you a non-exclusive, non-transferable, personal and limited right to access, use and display this Site and attendant materials for your personal use only. This authorization is not a transfer of title to the Site and materials contained herein and is subject to the following restrictions: (i) you must retain, on all copies of the Site and materials, all copyright and other proprietary notices of Kalmar; and (ii) you may not modify, distribute, transfer or store the Site or materials in any way or reproduce or publicly display or perform, or otherwise use the Site and materials for any public or commercial purpose, except as otherwise expressly permitted herein.
The contents of the Site are Copyright © Cargotec Finland Oy 2014. Any rights not expressly granted herein are reserved.
The trademark "Kalmar" and all other trademarks of Cargotec Corporation or its subsidiaries as well as product names, logos, commercial symbols, tradenames, slogans whether register or not, and services are trademarks of Cargotec Corporation. Your access to this Site should not be construed as granting, by implication, estoppel or otherwise, any license or right to use any marks appearing on the Site without the prior written consent of Cargotec Corporation.
Kalmar reserves the right to change or modify this Site or withdraw access to it at any time with or without notice.
The contents of this Site are provided on "as is" and "as available" basis. The use of any information, tools and services on this Site shall be executed on the user's sole responsibility and Kalmar makes no representations or warranties to the accuracy or functionality of such information, tools or services. Except as required by applicable law no warranty of any kind, either express or implied, is made in relation to the availability, accuracy, reliability or content of the Site.
Except as required by applicable law Kalmar shall not be liable for any direct, indirect, incidental, special or consequential damages, lost profits or for business interruption arising out of the use of or inability to use this service, even if Kalmar has been advised of such damages. Kalmar shall not be liable for any inaccuracies, delays or failures contained in this Site, and shall not be obligated to notify users when information has been updated. Kalmar is not responsible for any loss or damage that is caused by your reliance on any data or services contained in this Site or data that the user has input into this Site.
Kalmar assumes no responsibility and makes no representations or warranties whatsoever for material created or published by third parties that this Site has a link to.
The Kalmar Privacy Policy web page discloses how Kalmar will maintain and use any personal data provided by you when visiting this Site. For all other submission of information or content by you, the following terms apply.
By submitting information or material (such as feedback, data, answers, questions, comments, suggestions, ideas, plans, orders, requests or the like) to Kalmar, for example by e-mail or via this Site, you agree that: (i) the material will not contain any item that is unlawful, libelous, defamatory, obscene, pornographic, abusive, harassing or threatening, or otherwise unfit for publication; (ii) you will use reasonable efforts to scan and remove any viruses or other contaminating or destructive features before submitting any material; (iii) you own the material or have the unlimited right to provide it to us, and Kalmar may publish the material and/or incorporate it or any concepts described in it in our products without compensation, restrictions on use, acknowledgment of source, accountability or liability; and (iv) you agree not to take action against us in relation to material that you submit, and you agree to indemnify us if any party takes action against us in relation to the material you submit.
Copyright © Cargotec Finland Oy 2014
This Privacy Policy related to the kalmarglobal.com service of the business area Kalmar within the Cargotec Corporation ("Privacy Policy") provides you with general information on the processing of personal data of the business area Kalmar within the Cargotec Corporation and its employees, partners and affiliates ("Kalmar") related to this web site and the Kalmar.com service of Kalmar ("Site"). Please read this Privacy Policy carefully prior to accessing the Site. If you do not agree with this Privacy Policy we expect you to leave this Site.
Kalmar has endeavoured to take appropriate measures in order to protect any personal data provided through this Site. Please note however that there are always risks associated with providing personal data and no system of technology is completely safe. Kalmar processes your personal data in accordance with the Personal Data Act (523/1999) and other applicable personal data legislation.
Kalmar's aim is to ensure an as efficient and secure data processing as practicable. In addition, Kalmar seeks to develop the Site for a better quality and broader scope of services. Kalmar's goal is to produce cost efficient services recognizing your specific needs without you having to register separately to each of the different services provided at the Site.
Kalmar believes in openness in the processing of personal data and hopes that you carefully review Kalmar's Register Description, providing for specific information related to Kalmar' s processing of personal data. Once you register at the Site or have otherwise been assigned a specific identification code to access your accounts, we may request that you provide certain information. The purpose in collecting this information is to provide customized services and content meeting your specific needs and interests.
From time to time Kalmar may place information on your computer to allow us to identify users of the Site. This information is commonly known as "cookies". Cookies give Kalmar information on how and when the Site has been used, where the user is in the Site structure and helps Kalmar to improve the Site for a better service. Cookies are today commonly used on many web sites. If you do not wish to receive cookies, or want to be notified of when they are placed, you may set your web browser to do so, if such function is supported by your web browser.
The processing of personal data is based on your consent. You may at any time revoke your consent. As processing of your personal data is necessary for us to be able to provide you with our services and products, revoking your consent may lead to a situation where we cannot provide you with some or all of the services and products. The Site is technically divided into separate sections some of which may require us to collect more personal data of you while some may be used without processing any personal data.
Kalmar will not transfer any personal data outside Kalmar or its partners and affiliates. Due to the technical and practical requirements of the processing some of the personal data may be located at the servers of subcontractors or processed by subcontractors, which have agreed to the data processing standards of Kalmar. Kalmar may provide aggregate statistics about its customers, sales, traffic patterns, and other related Site information to reputable third parties, but these statistics will include no personal data.
You may at any time contact Kalmar to check that the personal data related to you is accurate. Kalmar will at your request rectify or erase any incomplete, inaccurate or outdated personal data. For more information, please contact Kalmar by sending an e-mail through www.kalmarglobal.com. As Kalmar seeks to develop the Site continuously, also this statement may be updated to correspond with the current situation. Kalmar reserves the right to amend this Privacy Policy and the linked Register Description and hopes, that you review this Privacy Policy from time to time for any amendments. Possible additional questions and comments about the activities of Kalmar as a data controller shall be directed to Kalmar via e-mail.